A Tale Of Two Mustangs
“For the time and money invested, there is no other airplane of this type that I would rather have,” said Paul Cox of Fort Myers, Florida. Without context, his opinion…
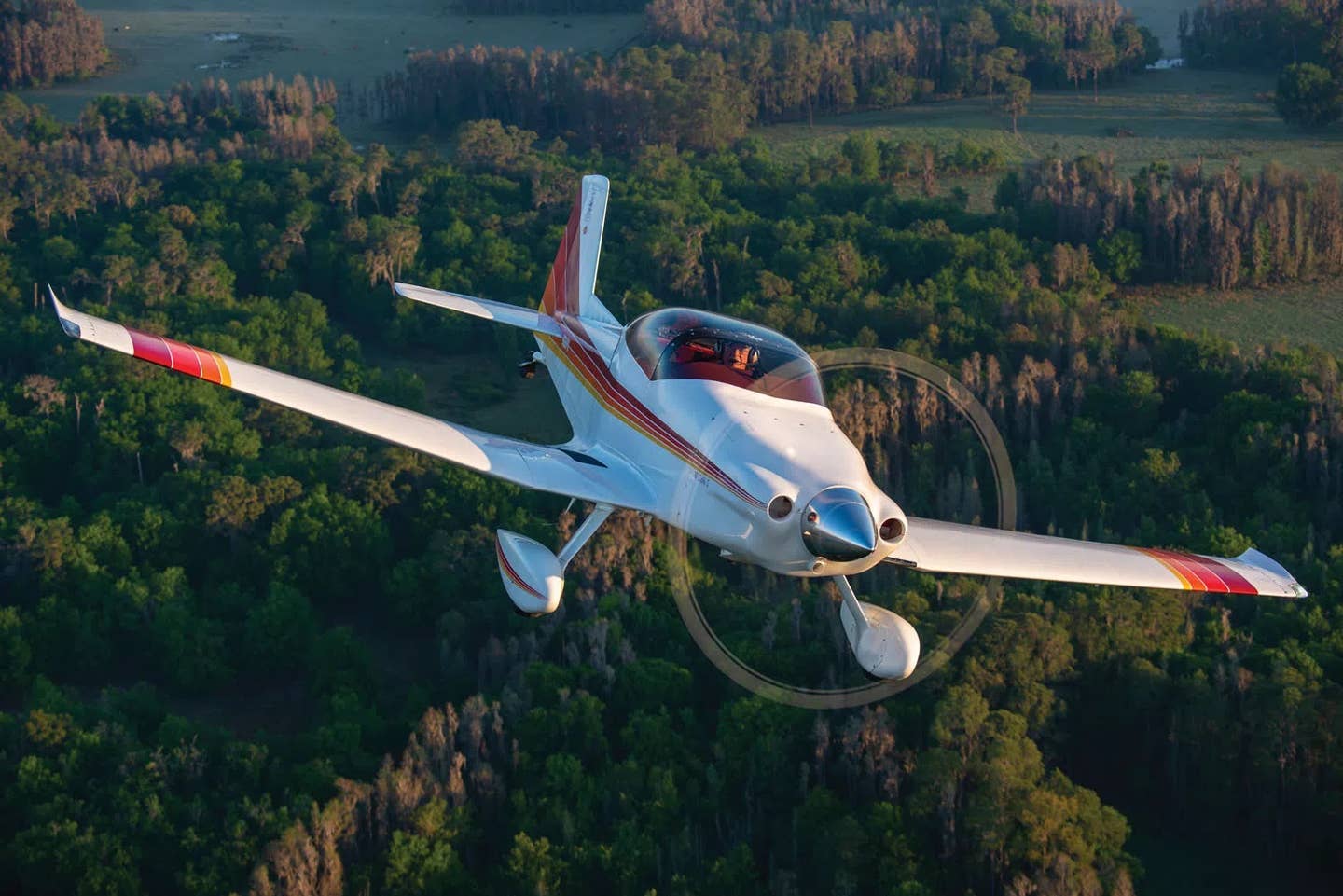
“For the time and money invested, there is no other airplane of this type that I would rather have,” said Paul Cox of Fort Myers, Florida. Without context, his opinion leans toward the homebuilder hyperbole side of the dial. The Experimental/Amateur-Built design he’s talking about is the Mustang II. He’s scratch-built two of them from the same 78 pages of plans he bought from the designer, Bob Bushby, in 1968.
When requesting N-numbers, Cox asks for the year he finished building the airplane. He was successful with his first Mustang, N72PC, in which he logged 1050 hours over 10 years. He sold it to build the second one with more fuel and horsepower and equipped so he could earn his instrument rating in it. “N86PC wasn’t available, so I had to settle for N80PC.”
Cox earned his instrument rating in 1989 and since N80PC’s first flight in 1986, he’s logged more than 3300 hours in the Mustang II he still flies a couple of times a week. “I’ll be 85 on my next birthday, in January, so you can imagine that I’ve slowed down a bit,” he said, adding that he hasn’t made many long flights for the past couple of years, since his wife of 63 years, Sara, can no longer climb into the cockpit.
“My wife gave me my initial flying lessons for Christmas in 1965,” Cox said, noting that their boys, Steven, was then 5 and Alan was little more than 18 months old. Now 61, Steven is a United Airlines captain flying internationally and a member of the Rocky Mountain Renegades, an airshow team flying Experimental/Amateur-Built airplanes, mostly RVs. Alan is a physician specializing in gastroenterology and practicing in his hometown of Louisville, Kentucky.
Flying magazine introduced Cox to the Mustang II, with its elegant, tapered laminar flow wings in 1967. “There wasn’t anything around like it except the Thorp T-18. The T-18 is not a bad airplane; I just don’t like square wings.” The Cox clan drove to Illinois in 1968 for EAA Rockford, specifically to examine Robert Bushby’s Mustang II. “I went back to Rockford in 1969, and Bushby converted it to tricycle landing gear. Like many homebuilt designers of that era, Bushby was giving rides to prospective builders.” Paul Cox was one of them. But having ordered the plans in 1968, he really wasn’t a prospective builder anymore.
Well Used Plans
“I ordered the plans, all 78 sheets of them,” Cox said. “I lived in Louisville, Kentucky, at the time. My buddy across town, Carl Bach, heard that I’d bought the plans, so we decided to build two planes at the same time. He built his on the east side of town, and I was on the southwest side of town, so we traveled back and forth inspecting each other’s work.” They built both planes from Cox’s set of plans, which also gave life to Cox’s second Mustang II.
“Carl made most of the form blocks for the ribs, bulkheads, instrument panel, firewall, and all that, and he let me use them. After you work with 2024-T3 [aluminum] for a while, you begin to like the stuff. At the end of the rib-building experience, I could make four ribs in an evening. Making the form blocks took longer than the parts,” Cox remembered, chuckling. “I made all the ribs, all the wing parts and a jig, and the first wing took me four months to assemble. The second one took me about two weeks. When you gain some experience, you can pick up speed,” he said.
“No kits were available at the time. Bushby offered some hard-to-make parts, but not like today.” For his second Mustang, Cox bought the leading edge skins from him. “With its wet wings, they were 32 thousandths, and it’s a lot tougher to bend them without any equipment. I also bought the extruded center section spar, and I built everything else.” His second Mustang wore a Glasair windshield in front of a cut-down Thorp T-18 canopy, and getting a good fit was the project’s most challenging task.
“Back in ’68, I bought all the sheet metal to build the first airplane for $225. I may have had to buy an extra piece because I cut something wrong,” Cox said. “I didn’t buy it from an aircraft supply company; I bought it from an aluminum supply company. They sold it to me by the pound, not the sheet. They didn’t stock it; they had to order it for me. It worked out real well.”
Carl Bach finished his Mustang in about three years, and Cox said his took nine months longer because “I was working a lot.” A retired automotive teacher, “I went to voc school when I was a kid and went to work for a Studebaker dealer when I was 16, doing new car service,” he said. “I worked for Studebaker dealers from 1953 to 1963. Then I opened my own shop, and I did that from ’63 to ’74. The school system wanted me to go work for them, and they came and got me basically, and I took it for the benefits. I took a cut in pay, but I also took a cut in work. I’ve been retired almost 25 years now.”
Finishing his first airplane in 1972, Cox made its first flight on July 4 at Freeman Municipal Airport (SER), across the Ohio River and 50 miles up I-65 in Seymour, Indiana. “It’s an old Army Air Force base with 5000-foot runways, where they tested and stored captured enemy aircraft during WW-II. I had about 200 hours of flight time and 2 hours of tailwheel time, and I’d flown with Carl Bach in his Mustang,” Cox said.
“Carl and I did a lot of formation flying and made all the fly-ins, Sun ’n Fun, Oshkosh and all the rest. He passed in 1990 with cancer. A professor in Lincoln, Nebraska, bought his airplane, and as far as I know, it’s still flying. With a buddy of mine, we took two airplanes out to deliver the Mustang to him.”
Cox flew his first Mustang, N72PC, for 10 years and 1050 hours, and then sold it to Leo Bush, “another Louisville guy who was a GE engineer.” Cox sold it to build a more capable airplane. “The first Mustang had a 150-hp engine out of a Piper Apache, later converted to a 160 with a fixed-pitch prop. It had 32 gallons of fuel, and I wanted more fuel for IFR,” he said.
Mustang Two
“I built the second Mustang because of my lust for the Glasair, but I couldn’t make that work with kids and college.” Using the same set of plans, Cox scratch-built it with IFR instrumentation, a 200-hp Lycoming IO-360 and a constant-speed prop from a Cessna Cardinal RG. “Some of the Mustang builders were starting to do wet wings, so I built a set that holds 37 gallons [total]. There’s a 14-gallon tank in the fuselage.”
Built before GPS, a Loran occupied the panel with King KX-155s and other avionics, including a TruTrak autopilot that “doesn’t do the fancy stuff like climb and descent, but it does everything else, and it works real good.” Cox replaced the Loran with two GPS units, a Garmin 496 portable and the big-screen iFly. “You can see it in bright sun; it’s fantastic!”
Steam gauges still populate the panel. “I’ve had three or four vacuum pumps over the years, but I’ve only had one steam gauge go bad in 35 years.” He’s also replaced three or four Maule tailwheels in addition to the usual consumables like batteries, brakes and tires. “I take a long look at everything when I do my annual condition inspections, and when anything else comes up in between.”
What became N80PC started life with a good friend of Cox’s, a fellow teacher who lived nearby. “We started building it together. He was also a teacher, and we got a lot of building done during a bad winter. On snow days, we’d build all day long. We built the fuselage (adding a fuselage door for the baggage compartment) and tail in four months from scratch. It was a lot of all-day work. Before it was finished, he sold it to another guy. The fuselage was on the gear, but there was no engine mount or anything like that. When that guy didn’t do anything with it, I bought it from him when I sold my Mustang.” Cox finished it in an oversize single-car garage that was about 30 feet deep and 12 or 14 feet wide.
In 1986, “the Louisville GADO [General Aviation District Office] made arrangements with the Indy office that let me take off from Louisville Bowman Field [LOU], a busy general aviation airport that was Kentucky’s first commercial airport and the oldest continually operating commercial airport in North America (it opened in 1921), and fly to Seymour, Indiana, for the test flights.”
IFR And Beyond
After completing the Phase I test time, Cox began working on his instrument rating in the Mustang. “Instructors would either love it or not touch it,” Cox said. “I got my rating in 1989, and the examiner asked if he could make several approaches while I was taking my checkride.”
Shortly thereafter, the Coxes and some of their EAA friends purchased a condo at Hilton Head, South Carolina. “My wife and I flew back and forth for long weekends. It was about 2.5 hours,” he said. “She loved to fly somewhere in the airplane, but to just get in and goof around, she didn’t go for that. We made a lot of trips to Hilton Head.”
Some of the more memorable trips Cox and his wife made were to Cody, Wyoming, with their Tiger flying friends for a Grumman fly-in. “And we flew to the Hangar Hotel in Fredericksburg, Texas, 70 miles west of Austin,” he said. “It’s on the Gillespie County Airport (T82). It looks like an old WW-II hangar, but it’s built new from the ground up.”
With the boys “all graduated and long gone, and with retirement looming,” in 1995 the Coxes purchased a lot at the Buckingham Airpark (FL59) in Florida. “We built a hangar home and made numerous trips between Louisville and Fort Myers during construction. I did a lot of the work myself, and it was 4 hours and 15 minutes nonstop. I had 51 gallons of fuel on board, and I usually had 10–12 gallons left when I landed. It is 730 miles nautical nonstop, and since I’ve moved down here, I’ve made the trip 55 times.”
Noting that he’s had some strange things happen over the years, “I probably shouldn’t tell you this, but our community is gated because Florida Mosquito Control is on the airport. When you push the button, it opens the remote control gate. It closes on its own; the button will not close the gate. So I’m taxiing one day, and the gate is open. I don’t know how long it’s been open; I don’t see any other airplanes in front of it. While I’m taxiing, I’m playing with my GPS—I should have stopped taxiing when doing that. Guess what, the gate closed on my prop, but it didn’t close far enough to get the cowl or spinner, but it destroyed the prop,” he said.
“You do stupid stuff like that sometimes. So I disassembled the engine and sent the crankshaft off and did all the proper stuff you’re supposed to do when the engine suddenly stops, and I got another prop,” he said. “I overhauled the engine at 2070 hours because it had a crack in the case. I overhauled the case, polished the crank and changed to a four-into-one exhaust system. That engine now has 3300 hours on it.”
This wasn’t Cox’s first hands-on efforts with a powerplant. When he was teaching, the school day ended at 2:30 p.m., so he’d then spend three hours building aircraft engines at Kentucky Flying Service “until the traffic rush hour was over.” He worked there pretty much full time in summer. “The owner was a WW-II guy who flew the hump. He was a good businessman. He had 51 airplanes and five helicopters. Everything was paid for, and he paid for the things I needed to get my A&P certificate. He’s passed since then.”
Cox and his wife had a more serious incident in 2004. They were flying to a brunch they used to hold “at that big [Florida] airport where John Travolta used to live with his airplanes,” he said. “I was making a crosswind landing to the 7000-foot runway, looking at the windsock—and the windshield disappeared. We hit a turkey buzzard. I didn’t see it because I was looking at the windsock, but my wife saw it and put up her hand. It busted her nose, split her lip and broke a tooth or two. We had blood and guts and feathers everywhere.”
Cox built the Mustang with a curved Glasair windshield, which was a little thicker than the stock one he had on his first Mustang. “The right half of it was missing, so I went ahead and slipped it in and landed. We called EMS and they came and picked us up and took us to the hospital. My wife was pretty banged up. It was the worst incident I had in the airplane.”
Mustang Competition
With a friend, Cox entered an AirVenture Cup race the year it ran from Denver to Oshkosh. “It was 777 miles nautical, so we had to run at reduced power to make it nonstop, but we averaged 212 mph (my figure), as fast as we could go without running out of fuel,” he said. “They wrote me down as a DNF—did not finish. The finish line was a fly-by of the Oshkosh tower. My race number was 36, and when we called in as Race 36, they probably confused us with the active, Runway 36.”
Cox entered the 2000 AirVenture Cup race from Kitty Hawk, North Carolina, and placed third in Class FX at 222.47 mph. “And that was at maximum gross weight with a passenger (Bruce Skaggs) and luggage. Some people raced and sent their luggage ahead with another airplane,” he said.
“Leaning on the fence at Sun ’n Fun 1997, a guy named Bruce Bohannon walked up and asked if I’d be interested in entering a time-to-climb contest,” Cox said. “I wasn’t prepared. The Mustang was fully fueled and filled with tools and other stuff, but I tried it. I was a finalist in ’97 and took second place in ’98. For the second contest, I had low fuel and I took out my tools, the right seat, and the extra radios. They say skinny wings won’t climb, but that’s not really true.”
Cox stopped flying IFR around the time his wife could no longer join him for their cross-country adventures. “I didn’t do any real bad weather like thunderstorms and icing—just low visibility and light rain. Once you get used to it, the Mustang is a fine IFR platform. A passenger might think the pilot is not doing anything because it looks like the pilot is not moving the stick. You can move the stick a quarter inch and you have a 45° bank. It’s a matter of getting used to it.”
While he’s not flying the hours he used to, Cox said he’s still having fun with his Mustang, flying locally once or twice a week, 30-minute hops for breakfast or lunch. As he approaches his 85th birthday, he said, “It’s like Dirty Harry said, ‘A man has got to know his limitations.’”
Bushby Mustang II
In 1959, Robert Bushby bought the rights and tooling for the Midget Mustang, the single-seat racer designed by Piper’s chief engineer after WW-II, and began selling plans and some parts for it.
Working from those plans, in 1963 he began work on the side-by-side two-seat Mustang II, which traveled by trailer for its debut at EAA Rockford in 1965. The prototype flew there in 1966. After developing and promoting the design for more than 30 years, Bushby sold the design rights to the Mustangs in 1992 to Mustang Aeronautics.
Led by Chris Tieman, Mustang Aero developed kits for the plans-built designs. Continuously updating the kits, including quickbuild options, the predrilled components and fabricated parts can be assembled with less than $1,000 of tools.
More than 400 Mustang IIs are flying today. For more information visit www.mustangaero.com.
Paul Cox Mustang II N80PC
- Kit price: Plans-built
- Number flying (at press time): 400+
- Powerplant: Lycoming IO-360, 200 hp
- Propeller: McCauley constant-speed
AIRFRAME
- Wingspan: 24 ft 4 in
- Wing loading: 16.5 lb/sq ft
- Fuel capacity: 51 gal
- Maximum gross weight: 1887 lb
- Typical empty weight: 1177 lb
- Typical useful load: 710 lb
- Full-fuel payload: 404 lb
- Seating capacity: 2
- Cabin width: 40 in
- Baggage capacity: 80 lb
PERFORMANCE
- Cruise speed: 210 mph
- Maximum rate of climb: 1900 fpm
- Stall speed (landing configuration): 58 mph
- Stall speed (clean): 62 mph
- Takeoff distance: 470 ft
- Landing distance: 680 ft
Specifications provided by the builder and Mustang Aeronautics.
For more great content like this, subscribe to KITPLANES!