On The Edge
Edge Performance of Notodden, Norway, has been around for little more than a decade, but their EFI and Rotax upgrades have quickly become popular, setting a high bar with race-quality…
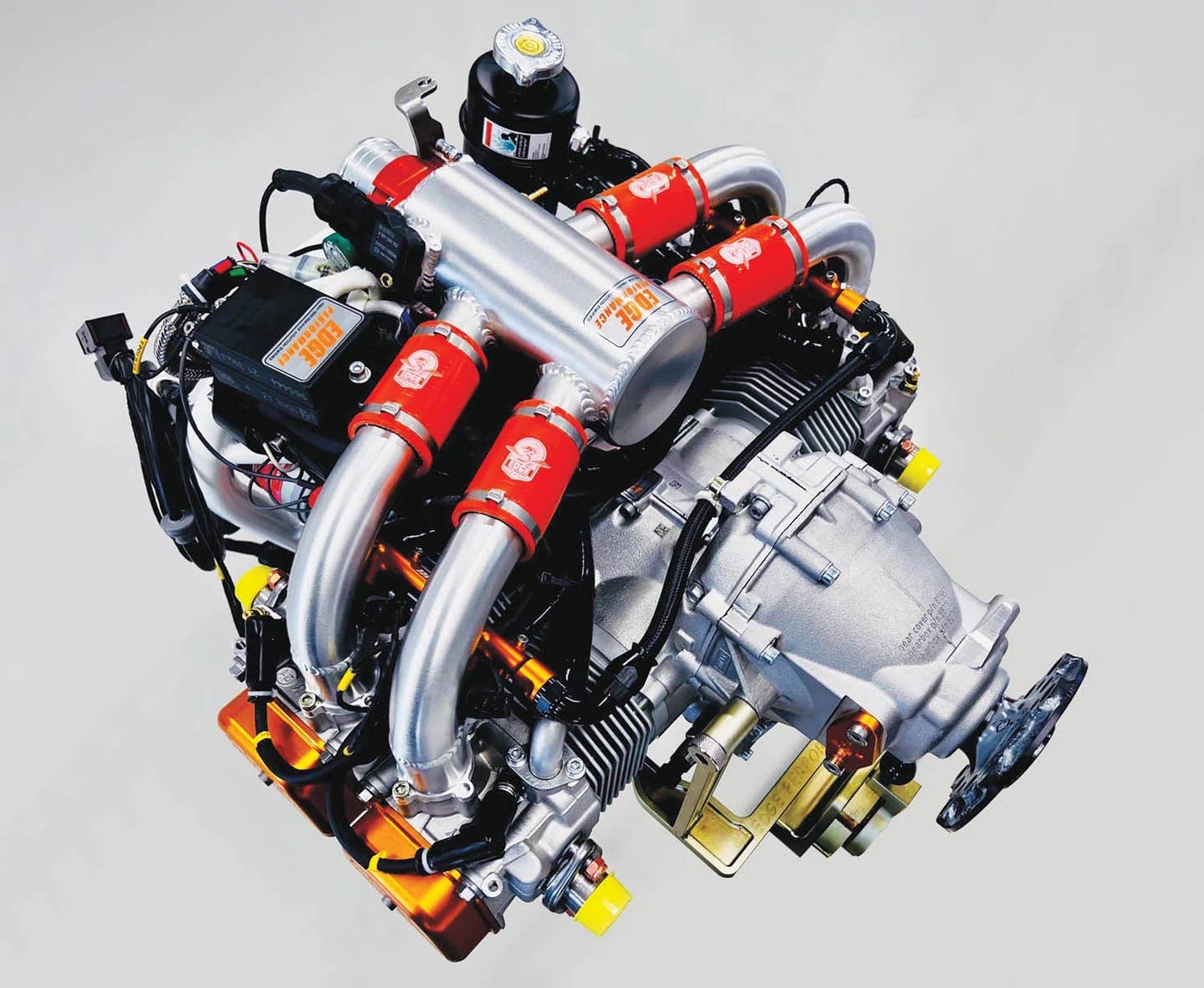
Edge Performance of Notodden, Norway, has been around for little more than a decade, but their EFI and Rotax upgrades have quickly become popular, setting a high bar with race-quality components. I’ll be putting the EP912sti in the SR-1 race plane—not only does it have exceptional power to weight (important given the 661-pound weight limit for the SR-1’s record category), but racers go best when it’s hot and high—and the EP912STi’s turbo ensures we can still make power in those conditions. Wanting to know more about the engine I was buying, I recently traveled to Notodden (a 90-minute drive west of Oslo) to learn more about the company’s background and processes.
Edge CEO and founder Thomas Hauklien has a long history with both Experimental aircraft and engine modification. He’s been an engineer for 15 years, having graduated with an electro-mechanical degree. His first plane was a RANS S-5 with a Rotax 503 two-stroke that he flew for about a year and a half. “I got to overhaul that engine. It seized up on me like most two-strokes.” This was followed by a Kitfox Model 4 he restored and flew for a couple of years with a Jabiru 2200 that he’d converted to a turbo. “That was kind of stretching it at the time, no one had ever done anything like that.”
This was followed by a Sonex with an AeroVee that Hauklien bought from the U.S., followed by another Sonex that he built himself. “Coming from a racing background, it bothered me that the engine produced too little power. So the first thing I did was get bigger-bore cylinders, bigger pistons, ported the heads and did regular tuning stuff to get a bit more horsepower.” This was followed by fuel injection and, finally, a turbo.
Appreciating that he’d pushed the Volkswagen-based engine too far—making a claimed 120–140 hp—Hauklien’s next step was to acquire an at-TBO Rotax 912. “Doing a full turbo and fuel injection for that one as well was only natural,” he says. Friends who were struggling with notoriously finicky Rotax carbs started to ask Hauklien to retrofit their engines as well, and from there word spread. In 2010 Edge attended AERO Friedrichshafen (think of it as Europe’s version of Oshkosh), “and that is when it really started to kick off,” says Hauklien.
“We got a lot of exposure [at Friedrichshafen]. At the time neither Rotax nor any of the other major brands were offering fuel-injected engines, so understandably enough there was a lot of skepticism among pilots. My argument was always if you go to the auto dealer today and buy a new car, would you have it fuel injected or would you want carbs that you have to maintain? The answer is simple. The next obvious question is how often does your car break down on the highway because the fuel injection system fails? It’s next to none. A lot of people approached us and said the Rotax has redundant dual ignition, and it has dual redundant fueling because it has two carburetors. Well clearly that isn’t the case. Basically you end up with double the risk of getting a carburetor failure and engine out because you have two carburetors, which both need to function perfectly in order to have an operating engine. If you lose one injector, it will still run on three cylinders. It will vibrate but you will maintain altitude. But if you lose one carburetor you lose one cylinder bank,” or half the engine, he says. Plus, injection eliminates the possibility of carb icing.
A Menu Of Mods
Edge has clearly gone beyond just fitting fuel injection to Rotaxes. The table below shows Edge’s available kits and upgrades, starting with straightforward big bore/EFI kits up through highly experimental mega-hp conversions of 1000cc motorcycle engines. (Note that although EP’s conversions start with a factory-new Rotax engine, its mods void any Rotax warranty and Rotax no longer considers these engines as Rotax.) The common thread among Edge’s engines is a conversion to its EFI, substitution of the intake/throttle body and for the relevant models, a turbo upgrade. The invisible part of the upgrade though is equally important: tuning.
“We have our own optimized intake and induction system that has been flow optimized, trying different runner diameters and lengths,” says Hauklien. “Inside the plenum the velocity stacks use a trumpet mouth to accelerate the airflow and keep it laminar, all of which has been meticulously tested on the dyno. But it’s always a compromise with tuning, regardless if it’s header or intake tuning. So rather than just focusing on making peak power, which is easy, we’ve always tried to focus on the rpm range where the engine typically operates. This is also really evident in dyno testing: We took a stock 100-hp carbureted 912 and it made 100.2 hp on our dyno. We then bolted on our intake and EFI system and it made almost 109 hp. With carburetors you have the venturi, so you get a pressure drop. But running EFI with a shaftless throttle body, we have no pressure loss whatsoever,” he says.
Here To Stay
Hauklien says that to date EP has sold approximately 300 engines, 2500 fuel injection kits, 300 big bore kits and approximately 30 EPeX Yamaha conversions (with North American dealer Jason Busat of BadAss PowerSports having assembled a handful of Epexes as well). Clearly, the company is expanding (they added their fourth employee in June), but it’s still relatively young and it’s not unreasonable to ask if they’ll be around in another 10 years to support these custom engines.
So where does Hauklien see the company heading? “If we can make it faster, stronger, lighter, we’ll continue to do so. The big question mark is the electrification of aviation in the future,” he says. “What is that going to do to our existing market? There are 60,000–80,000 Rotax engines flying worldwide, and they’ll continue to do so for decades. It’s not like people are going to throw out mid-time engines and replace them with factory fuel-injected engines, because they are getting so expensive now that it makes more sense to retrofit a fuel injection kit even if it’s a midlife engine. So I think there is a huge aftermarket for decades ahead for us.”
While support is important to customers and a steady business in core modifications is key, that’s not all that Hauklien is about. “What drives me now and motivates me to come to work in the morning is working on the R&D projects. We’ve done one-off helicopter engines, gyrocopter engines and UAV engines. I’m really dedicated to working on R&D and the engineering side of things. Hopefully as we continue to grow with increased staff, I can step back and spend more time on what I enjoy doing, which is development, improvements, testing.”
When asked if Edge was married to the Rotax core, Hauklien pointed out that for him, it’s the only engine that makes sense to be modifying or servicing. Edge offered turbo kits for the Jabiru four- and six-cylinder engines but discontinued them due to anemic demand (though he still stocks parts to service existing customers). There are only a couple of ULPower engines in Norway, and Hauklien doubts that there’s much he could offer on an engine that is already EFI and has a turbo version as well. Yes there is a decent market in EFI retrofits on conventional, large-displacement aircraft engines, but he sees SDS and FlyEFII (for which Edge is a European reseller) as already doing a good job supporting that market.
One Big Question
So let’s get to the elephant in the living room: How does Rotax feel about Edge modifying their engines? “We get asked that a lot,” laughs Hauklien. “It’s a funny story. Until three or four years ago, we had a quite intense relationship with Rotax. They obviously didn’t fancy what we were doing because they were obviously afraid of us hurting their brand and reputation for reliable engines with our modifications, which is understandable. What was funny, though, was that every time we went to an exhibition the Rotax salespersons would give us the most intense stares. Meanwhile the young engineers from Rotax came by and really appreciated the work we had put into the engine. They would say, ‘Why didn’t we think of this, what clever solutions!’ That was always fun for us to watch. I think Rotax just got fed up with all the local NTSBs approaching them who would say, ‘We have a Rotax engine with this serial number and there was a crash, it had an engine failure, we need you to investigate it, we need a statement from BRP [parent company Bombardier].’ And obviously as soon as Rotax got pictures from the site or the wreckage, they could see that it was a modified engine.”
The solution was straightforward. “Eventually what we agreed with Rotax in order to buy engines and parts unrestrained was that we remove any part from the engine that clearly states Rotax, like the valve covers and the Rotax serial number plate, and we install our own plates,” continues Hauklien. “However, we do maintain the original Rotax serial number so that the owner is able to follow up in terms of service bulletins. That took out the headache from Rotax if ever there were an accident. I’m not sure if they really like what we are doing, but it’s gotten to the point where we’ve gotten so much recognition and proven that we can make stuff reliable.”
Which raises the question: Why doesn’t Rotax just make these improvements themselves? “Well, they kind of have,” says Hauklien, pointing to the 912 iS and 915 iS. “But it probably doesn’t make sense for them financially to make retrofit kits. I think it has a lot to do with cost. It is directly comparable with the automotive industry. Making high-performance racing parts is tedious, time-consuming and expensive. It is exactly what OEM manufacturers want to avoid.”
Interestingly, even though Edge is not an official Rotax dealer, they receive discounts, support and training from the Rotax dealer in northern Europe. Hauklien ventures that they are one of Rotax’s biggest customers. He sees this as beneficial, since it gives Edge the freedom to work on engines as they see best. And he sees an advantage for Rotax as well. “Because we acquire a new engine from Rotax and modify it, it’s not like they are losing out on sales. We are in a way beneficial to them. From Rotax’s perspective, they get a sale but they get to take out liability, because we are carrying the liability now, it’s an Edge Performance engine. So that is an easy-money, trouble-free, no-liability sale [for them].”
Beyond The Mods
It should be noted that engine modifications are only half of Edge’s business. They also perform annual inspections, maintenance and repairs for European ultralights (a category akin to Experimental in the U.S.), teardowns and overhauls of Rotax engines, and are resellers for a number of European brands such as Shark.Aero, TL-Ultralight, Eurofox and Zlin. They are also authorized dealers for Garmin avionics, Beringer wheels/brakes, and quite a few propeller brands including Airmaster, Woodcomp, Duc and Noah. “We do everything. It’s not Aircraft Spruce, exactly, but we are the only ones who keep those parts in stock here in Norway,” says Hauklien.
Even with the growing success of his business, Hauklien remains an avid pilot. The Sonex was followed by a 200-knot Shark, a glider license, an instructor’s license for both gliders and ultralights as well as multiple other ratings. Since those humble RANS S-5 beginnings in 2006, Hauklien has racked up 3500 hours of flight time in all manner of aircraft. He was Norway’s aerobatic Sportsman national champ in 2019 and just won the 2022 Intermediate national championship flying the Extra 300; his current ride is an RV-4 with inverted oil. Hauklien is also building an Experimental Norden Cub with the 300-hp EPeX300Ti and also has on order a Shark Turbo to be powered by his EP912STi. Which is all to say that Hauklien is not just an engine builder, he is an avid pilot who flies—and test flies—behind the engines he’s built.
• Edge previously offered turbo and fuel injection kits for both the four- and six-cylinder Jabiru engines but discontinued due to a lack of demand. They still stock parts to service customers who purchased these kits, however.
• Edge does not offer customer-installed turbo kits due to the skills required for a safe installation.
Speed Round: Technical FAQs
KITPLANES: How do your engines compare weight-wise with stock Rotax?
Edge Performance: Fuel injection is typically 3 pounds lighter than carbureted. And our EP912STi is typically 11–15 pounds lighter. That comes from using thin-walled tubing on the intake, rather than heavy cast parts. We have four injectors (ounces) rather than two carburetors (2 pounds each), one air filter rather than two and a dual electric pump unit that is lighter than the stock electrical/mechanical pumps.
KP: What type of fuel do you recommend for your engines?
EP: We definitely recommend unleaded mogas. In the U.S., that would be premium 91–93 octane. In Europe we have UL91 and UL96 unleaded avgas. Although leaded avgas is recommended neither by us nor by Rotax, if you are doing cross-country sure enough you are going to have to fill with avgas every now and then, but the EFI doesn’t actually care about the leaded fuel.
KP: How about fuel with ethanol added?
EP: E5–E10 is fully compatible with all our engines.
KP: How does EFI improve vibration levels and fuel consumption in Rotax engines?
EP: You are always going to struggle with the carburetors staying in sync. Our tuned four-into-one intake runs much smoother throughout the entire rev range and it idles much better. In addition, we can tie fuel injection to valve opening time. With a carburetor, fuel will puddle in the intake because there are pauses between every cycle. Timed injector openings deliver atomized fuel just as the valve opens. That helps with both smoothness and brake specific fuel consumption.
If you do a lot of cross-country flying, you are going to experience better fuel consumption. The Bing carburetors altitude-compensate somewhat up to 5000–6000 feet, but after that your EGTs will be dropping like crazy and you will typically experience that as a stained and sooty belly. Our fuel injection monitors the barometric pressure and adjusts the fuel accordingly.
KP: What are you doing to make sure that these engines can withstand the increased power output?
EP: EFI generally increases the lifespan of an engine because it’s running more efficiently with the optimized mixture. You’ll have less deposits in the engine, less valve and piston wear and less vibration. If we look at the high-performance engines, we replace a lot of the engine internals. We use forged pistons, we weld the crankshaft, install piston oil squirters, a bigger oil pump and more. These are modifications that we’ve implemented one by one over the past few years based on experience, field reports and engine teardowns.
If operated within the limitations and maintained properly, these engines have a fair chance of reaching TBO. However, we do emphasize that the high-performance engines in particular are run “on condition.” That means in addition to following regular maintenance, you should do a leakdown test every 100 hours, oil analysis, etc. Basically it boils down to keeping an eye on the engine, not just pouring in new oil, replacing the filter and going back out to fly.
KP: Do you modify the gearbox for the increased power output?
EP: Yes we do, slightly. We increase the preload of the clutch assembly just enough for it to do its job if you have a prop strike and to absorb torsional vibrations or harmonics, but to not slip.
KP: Increased power means increased heat rejection. Is the stock cooling system adequate?
EP: I would say in 85% of installations the factory coolers should be adequate. My experience is that most people don’t use the increased power continuously. It’s more for short takeoffs, quicker climb and maintaining power at altitude. But depending on where you live, you may have to install bigger oil coolers or radiators to be able to dissipate the additional heat that the engine develops.
KP: Are your engines reaching TBO?
EP: Yes. On the first engines we did teardowns at 200 hours, then 500, 1000, 1200, 1500 and then a couple of engines that reached 2000 hours. Most of our engines are in STOL planes, and it’ll take 10 or 15 years to reach TBO. So it’s mainly engines in OEM airframes that have managed to accumulate flight hours quickly. There are occasionally findings of interest, for us to see what we can improve on or at least relate to existing customers in terms of a service bulletin, say.
KP: Do you offer a warranty?
EP: Yes. Our factory new engines are 1 year/200 hours and fuel injection kits come with a five-year warranty.
This article originally appeared in the February 2023 issue of KITPLANES.
For more great content like this, subscribe to KITPLANES!